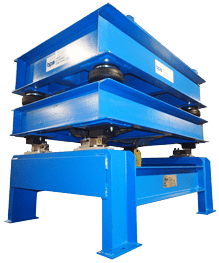
BPS’s vibratory table construction is the long-lasting, built-to-spec solution you’ve been looking for. Tackling challenges in your facility like condensing, settling and packing, our vibratory tables deliver the low-maintenance and consistent operation you need. Whether you’re de-airing concrete or densifying industrial materials for shipping, you will receive the vibratory table specific to your needs with our flexible design options.
Use Vibratory Tables to settle product contents in Drums, Bulk Bags, Portable Bins, Bulk Boxes, Gaylords, Lever Packs, and Molds. Browse through our Vibratory Table models by clicking the name on the list below. For more detailed information please contact us.
Use our contact form to get a quote or call BPS at 330-220-1440