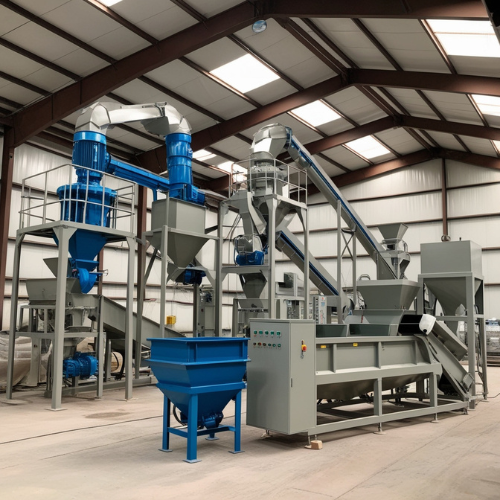
We take pride in our innovative solutions, design, technology, manufacturing, installation and service for everything from our Bulk Bag Fillers to Vibratory Feeders and Pallet Destackers. BPS’s commitment is to provide its customers with state-of-the-art technology and service of the highest quality. Our personnel has over 100 years of combined experience, and that experience is evidenced by the design and equipment selection for your specific application. Our systems are not built to a “cookie cutter” standard but are designed around individual customer requirements. Each phase of the project is professionally monitored to ensure complete customer satisfaction. Understanding our customers’ needs and expectations is the key element of our success and continued customer loyalty.
Use our contact form to get a quote or call BPS at 330-220-1440